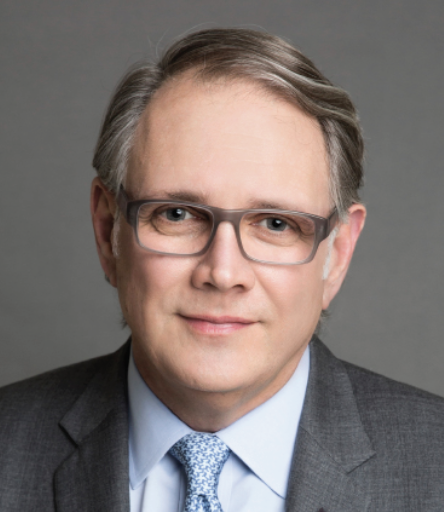
Dennis Darby
CEO, Canadian Manufacturers and Exporters
Canadian manufacturers are facing serious long-term labour pressures that governments must start responding to now.
Finding a sufficient number of skilled workers has been an ongoing challenge for Canadian manufacturers. Although the sector has come out on the other side of the difficult pandemic-related labour force disruptions, the challenge of labour and skills shortages is not going away anytime soon.
Manufacturing sector challenges
Canada’s population is rapidly aging, with baby boomers retiring out of the workforce in large numbers. In 2023, 27 per cent of factory workers were aged 55 years and over, up sharply from just nine per cent in 2000. As a result, the manufacturing sector is expected to see 40,000 retirements per year between 2024 and 2031. Putting it in more stark terms, 15 per cent of Canada’s current manufacturing workforce is expected to retire over the next eight years. At the same time, not enough young Canadians are choosing to pursue a career in manufacturing, limiting new entrants into the sector’s workforce.
The greying of Canada’s manufacturing workforce is a serious threat to the long-term growth and success of the sector. “An increasingly greying workforce has serious implications for the manufacturing sector and the broader economy,” says Dennis Darby, CEO of CME. The aging of Canada’s population all but guarantees that Canada’s employment rate — the percentage of the population that is employed will decline in the coming years resulting in a lower standard of living for Canadians.
CME is calling on the federal government to put more focus on the intake of economic class immigrants to help address long-term labour pressures.
One way for Canada to counter the coming wave of retirement is to improve business investment and labour productivity. However, on this front Canada’s recent track-record has not been encouraging.
The challenge Canada is facing can be illustrated by looking at investment per worker, a common metric that shows the extent to which the average employee is getting equipped with new capital that can raise productivity and enhance competitiveness relative to workers elsewhere. Unfortunately, investment per worker in the manufacturing sector is three times lower in Canada than in the U.S.
As a direct result, Canadian factory workers are much less productive than their American counterparts. In 2022, output per hour worked in the U.S. manufacturing sector was $87.4, whereas it was only $51.6 in Canada’s.
Action is needed
To address the long-term skills challenges facing the manufacturing sector, CME recommends the following:
1. Focus on economic class immigrants and build more housing
“CME is calling on the federal government to put more focus on the intake of economic class immigrants to help address long-term labour pressures,” says Darby. However, for Canada to continue to bring in the skilled labour our manufacturers need, we must do more to ensure our communities have sufficient housing available. All levels of government need to work together to tackle Canada’s acute housing shortage, so that new Canadians and workers will be able to find affordable housing near manufacturing jobs.
2. Increase the employment of youth and underrepresented groups
The government could renew and increase funding for programs that encourage youth and persons from underrepresented groups, such as women, people of colour, Indigenous people, and newcomers, to seek a career in manufacturing. With youth representation three times lower than it was in 1976, more needs to be done to attract this group to the trades by introducing and expanding apprenticeship programs and incentives. To support other underrepresented groups, government can and should increase inclusion programs and awareness campaigns such as CME’s Women in Manufacturing initiative, which aims to increase the number of women in manufacturing by 100,000 by 2030.
3. Invest in automation and advanced manufacturing technologies
Capital investment in things like machinery, equipment, and software is strongly correlated with higher productivity. The government should be encouraging businesses to invest in these productive assets by accelerating and incentivizing investments in the technology and manufacturing sector. “New technologies can lead to a wide range of potential benefits like lower operating costs, increased product quality, higher innovation capacity and increased customer satisfaction,” says Darby.
The manufacturing sector can’t solve this problem alone. Industry, government, and other stakeholders need to work together to expand the labour pool and invest in automation so the sector can grow and thrive. Visit cme-mec.ca to learn more.