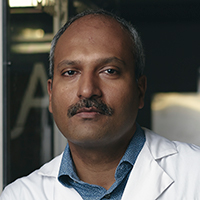
Dr. Ravi Selvaganapathy
Director, CEPEM, Engineering Professor, McMaster University
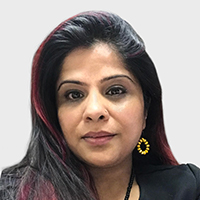
Vani Kshattriya
Director of Marketing & Global Quality, RONCO Safety
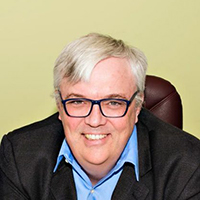
Dr. Darren Lawless
Assistant Vice-President, Research, Innovation & Partnerships, McMaster University
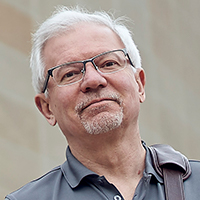
Dr. John Preston
Associate Dean, Research & External Relations, Faculty of Engineering, McMaster University
The Centre of Excellence in Protective Equipment and Materials provides companies with expertise, design, and testing to help develop superior, Canadian-made PPE.
There was a point early in the COVID-19 pandemic when Hamilton hospitals had only a week’s supply of face masks left. A shortage of personal protective equipment (PPE) in Canada, along with export restrictions by China — which supplied about half of the world’s PPE — had created a dire situation.
Looking for a solution, Dr. Alison Fox-Robichaud, a critical care physician at Hamilton Health Sciences and a professor of medicine at McMaster University, reached out to members of McMaster University’s Faculty of Engineering for help — and the work began.
“Immediately, our team of engineers began examining their capabilities to manufacture a supply of masks and face shields,” says Dr. John Preston, associate dean, research & external relations at McMaster’s Faculty of Engineering. “They quickly realized the magnitude of the challenge, which included a lack of manufacturing capacity in Canada as well as a shutdown of access to testing facilities in the U.S. to Canadian companies.”
Dr. Preston says time was of the essence, so with little delay, the team set up a facility to assess filtration materials for breathability, filtration efficiency, and fit. They also recruited local manufacturers who could repurpose their facilities to produce PPE. By the end of June 2020, and with a team of about 20 faculty members and 50 research staff and students, the Centre of Excellence in Protective Equipment and Materials (CEPEM) was created.
A home-grown hub for research and development
“We designed the centre to be a hub for companies interested in this area, to enable a research and development program and translate those findings into products that Canadian industry would put out into the world,” says Dr. Ravi Selvaganapathy, Director of CEPEM and a professor of mechanical engineering and biomedical engineering at McMaster.
Since March 2020, CEPEM has worked with more than 50 companies to identify suitable materials, design prototypes, and develop validation tests. These companies include athletic garment maker Niko Apparel Systems, which is producing more than 20,000 hospital-grade surgical face masks a day, and automotive parts manufacturer Woodbridge Foam Corporation, which is producing a level 3 surgical mask.
Another CEPEM partnership is with Concord, ON-based RONCO Safety, which has been a leading manufacturer of PPE, including safety glasses, disposable gloves, earplugs, masks, and gowns, since 1996. RONCO worked with McMaster in 2017 to develop a protective technology for a new glove, filing a joint U.S. patent for its technology in 2018. The following year, they worked together to develop innovative technologies for incorporation into disposable face masks. In 2020, RONCO extended that partnership to develop next-generation face masks with improved protection, comfort, and fit.
With assistance from CEPEM, RONCO’s establishing a laboratory to test materials for face masks and other PPE, under the leadership of Dr. Dariush Firouzi – initially part of Dr. Selvaganapathy’s team at McMaster and now RONCO’s Architect of New Innovations.
Bringing manufacturing back to Canada
In August, the Ontario Together Fund invested $1.5 million to help RONCO establish the production capacity to manufacture surgical masks and respirators at its Ontario plant, replacing production that had been happening in China. The company has two surgical mask machines running at full capacity to make more than three million masks a month and will soon add two N95 respirator production lines — each producing a different style.
“We always planned to bring our manufacturing back to Canada. The pandemic accelerated this for us,” says Vani Kshattriya, RONCO’s Director of Marketing and Global Quality. “McMaster and CEPEM were involved with us through this entire project of developing and manufacturing these masks in Canada. Very important for us is the next-generation filter material, which is able to provide protection for a longer period of time.” Kshattriya says RONCO will continue to work with CEPEM to increase the efficiency of its production line. “We’re working with them to take it to the next level and make sure we’re producing good-quality PPE at an efficient level,” she says. “Demand for PPE goes up every day and we need to do our best to support this and ensure we don’t depend on any outside country for our needs. Made in Ontario — we’re very proud of this.”
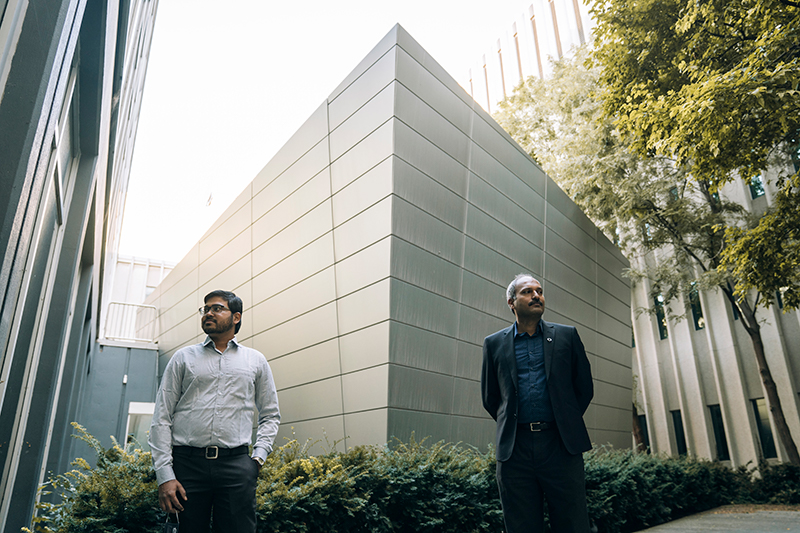
Planning for a future after COVID-19
Dr. Selvaganapathy admires RONCO’s foresight for investigating these technologies even before the pandemic. “The emphasis right now is on bringing manufacturing back to Canada. The centre is interested in keeping this industry sustainable within Canada even when the COVID-19 crisis goes away. We want to make sure that Canadian companies can create value-added, next-generation products,” he says.
“Supply chains have become very global for the past 20 to 30 years,” Dr. Selvaganapathy adds. “That works well in times where there’s no crisis. But there’s now a realization that capabilities have to reside in this country so we can respond to these shocks much more effectively.”
Supply chains have become very global for the past 20 to 30 years,” says Dr. Selvaganapathy. “That works well in times where there is no crisis. But there is now a realization that capabilities have to reside in this country so we can respond to these shocks much more effectively.
Dr. Selvaganapathy
CEPEM focuses on six key areas: designing and developing PPE, advanced manufacturing, research in functional materials, testing and validation, creating Canadian standards for PPE, and making PPE more sustainable for the environment.
“We’re at the birth of a new industry in Canada with PPE design and manufacturing” says Dr. Selvaganapathy. “Through research and development and with expertise from across engineering, sciences, and health sciences, we want to create next-generation PPE, which hasn’t been done anywhere else in the world.”
Dr. Darren Lawless, McMaster’s assistant vice-president, research, innovation & partnerships, says that these kinds of collaborations are critical to advancing the country’s innovation capacity. “Partnerships are in McMaster’s DNA,” he says. “We’re recognized as a trusted and valued partner by governments and industry, and continue to attract more corporate funding than any other university in the country.”
CEPEM is part of Canada’s Global Nexus for Pandemics and Biological Threats, an international network of experts working to prevent pandemics and mitigate global health threats which is headquartered at McMaster.