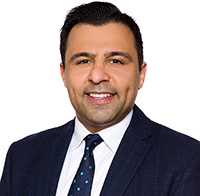
Ajay Kochhar
President, CEO, and Co-Founder of Li-Cycle
Li-Cycle’s innovative battery recycling process is transforming how we deal with electric vehicle lithium-ion batteries.
Today, one technological shift is changing the future of transportation – electric vehicles (EVs). This movement towards clean, sustainable transport is leading automakers to quickly ramp up EV production.
As the world’s largest economies continue to encourage electrification and the mass adoption of lithium-ion batteries – which power EVs – it’s becoming increasingly imperative that our planet also has a sustainable solution in place to support recycling at every stage of the lithium-ion battery lifecycle.
That’s where Li-Cycle comes in. Since its inception, Canadian company, Li-Cycle, has created a sustainable and scalable solution to strengthen the EV battery supply chain by recovering up to 95% of all materials, including battery-grade lithium, nickel and cobalt, found within spent lithium-ion batteries.
By 2030, over 15 million tonnes of lithium-ion batteries will become available for recycling. That’s a lot of material — hundreds of football fields. You don’t want that going into landfills.
Prioritizing sustainability
Li-Cycle co-founders Ajay Kochhar and Tim Johnston met while working at a global engineering firm. “This is where we became lithium-ion battery geeks,” says Kochhar. “We were constantly wondering what was going to happen to all these batteries being made when they reached end-of-life. We were also aware that the way they were made wasn’t perfect. Those big questions inspired Tim and I to get into the space.”
In 2016, Kochhar and Johnston launched Li-Cycle, one of North America’s leading lithium-ion battery recycling companies. To date, Li-Cycle’s innovative Spoke & Hub Technology has achieved a growing list of significant milestones and accomplishments. From Li-Cycle’s first mini-pilot in Canada to the launch of its demonstration Spoke in Kingston, Ont., Li-Cycle has now successfully scaled to a total of three Spokes, with more on the way across North America and Europe. Li-Cycle’s first North American Hub, located in Rochester, NY, is also on track to be commissioned in 2023 with the capacity to process battery material that is equivalent to approximately 225,000 EVs per year.
Game-changing technology
Li-Cycle’s proprietary Spoke & Hub Technology is a two-stage process that can recycle all types of lithium-ion batteries – from EVs to laptops – regardless of their chemistry or form factor.
“The Spokes are decentralized facilities where we mechanically break down the batteries safely,” says Kochhar. This overcomes logistics challenges — EV batteries are very large, and it’s not practical to transport them around the world. “The second and final step is the Hub, which is a chemistry process wherein we take the intermediate products from the Spokes,” continues Kochhar. “They then go back to battery-grade raw materials, like lithium, nickel, and cobalt. We call it urban mining. These materials go on to our commercial partners, like LG Chem, Glencore, or General Motors.”
Creating a cleaner world
The entire process involves minimal wastewater production, no direct emissions, and substantial net environmental benefits via indirect greenhouse gas emissions reduction. Most importantly, Li-Cycle’s process maintains zero waste diversion to landfills.
“By 2030, over 15 million tonnes of lithium-ion batteries will become available for recycling,” says Kochhar. “That’s a lot of material — hundreds of football fields. You don’t want that going into landfills.”
Fortunately, Li-Cycle has taken up the challenge of dealing with these batteries, and of providing a sustainable end-of-life pathway for lithium-ion batteries.